Our company is a professional manufacturer of auto parts. The main products are mostly shafts, large batches and varieties (as shown in Figure 1). The product supply schedule is urgent and the product quality requirements are strict. In order to meet the market requirements, in the machining process, CNC lathes are used for processing. In the past production, the traditional operation method is to first face the knife with B, input the Z-direction tool to complement the value, cycle start to complete the turning of the B-face and the outer circle of the flange; and then input the Z-knife complement value with the A-facing tool. The cycle starts to complete the turning of the rod and C face (the end faces and the center hole are processed in advance). There are some problems in the actual implementation of this method: due to the manual tool setting, the difference in personal skills has a great influence on the product size; the knife marks on the knife surface are different, which affects the surface quality; each product needs Manual tool setting increases the auxiliary machining time and is prone to collision. It requires high skill for the operator. The tool cuts in the oxide layer with higher hardness on the surface of the blank when it stays in the tool setting and exits in the X direction. , reduced the use of the tool to order.
With the rapid development of China's economic construction, some changes have taken place in the human resources market. Most enterprises have difficulty in recruiting workers, especially CNC lathes with skilled skills. The method of relying on personal skills to ensure product quality has not adapted to the current state of modern production. Combining with the problems in the past processing, we have developed a reasonable processing route and simple operation method, relying on the advantages of process equipment and equipment performance to ensure product quality, improve product processing efficiency, and reduce the operator's operational difficulty. a problem. After detailed argumentation, a new process is formulated based on the current situation of the company:
(1) Mill the A and B end faces with the center hole B4 based on the outer circle and the B end face of the D and E sections.
(2) The B-end face and the D-outer circle are machined on the A-plane, the E-outer circle and the B-end center hole.
(3) The outer circumference of the E and the end of the C are machined on the B side, the outer circle of the D and the central hole of the A surface.
In this process route, the process 1 adopts the center hole milling end face machine tool, and the two end faces are controlled by the B end face as the reference to control the full length size, and the center hole at both ends is used to provide the processing reference for the subsequent processing; the process 2 is processed by the numerical control lathe. The surface A is an axial positioning reference, which can ensure the accuracy of the workpiece coordinate system and the machine coordinate system, so that the position of the subsequent machining parts after assembly is unified, which provides a guarantee for the NC toolless operation. The first piece of workpiece is machined in the axial direction with the B end face to the tool input value to process the B end face and the D outer circle. After the measurement and verification and fine adjustment of the post-cure procedure, the subsequent workpiece can be cycled and started only after the same clamping. machining. In this process, although the outer circle of the E portion is an unprocessed blank surface, the axis thereof does not completely coincide with the axis of the central hole of the A end after re-clamping, but it is away from the processed portion and coincides with the clamping portion of the upper process, after processing The machining reference of the B-end and D-outer circles is mainly the B-end center hole, and the small-end reference is actually an auxiliary reference. The amount of runout of the surface of the machined surface to the center hole at both ends can be controlled within 0.1mm to meet the product pattern requirements. The small end of the product has a small diameter and cannot be directly positioned by the end face of the chuck. It is necessary to add a positioning sleeve (see Fig. 2), the opening is provided for the claw to pass, the outer diameter is matched with the inner hole of the chuck, and the inner bottom surface is the positioning surface. This device ensures stable positioning and smooth clamping of the workpiece. In the process 3, the flanged machined surface D is used as the reference for positioning, and the B-end center hole is completed in one clamping; the B-end is used as the axial positioning reference, and the A-end adopts the top positioning, and the debugging and processing methods and processes 2 is the same.
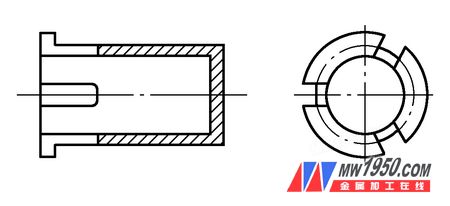
Figure 2 positioning sleeve
This process operation method has been verified in production. After practice comparison, the tool marks generated by the tool are eliminated; the dimensional instability caused by the tool error is eliminated; the cutting layer is below the workpiece surface when the workpiece is cut. The metal substrate eliminates the abnormal wear and impact of the tool during the tool setting process, and improves the tool life; the machining time is shortened due to the reduced tool setting step, and the machining efficiency is improved; more importantly, the operation is improved. The work performed by the personnel is only the correct assembly of the workpiece and simple equipment maintenance, which greatly reduces the skill requirements of the numerical control operators. After the process is determined, the general personnel can be employed after simple training, and the product quality is stable, and the single person can control 2 ~4 sets of equipment have greatly improved production efficiency and solved the problem of difficult employment for enterprises.
Due to its numerical control principle, CNC machining has good dimensional stability and high repeatability. It is suitable for batch and high-volume product processing, but it has certain skill requirements in operation and programming. In the process of compiling the process, we should foster strengths and avoid weaknesses. In combination with the company's own situation, we should try our best to simplify and simplify the factors, and use unfavorable factors as favorable factors to process qualified products at the lowest comprehensive cost and strive for more profit space for the enterprise.